Perspectivas de trabajo y oportunidades derivadas de la implantación del vehículo eléctrico
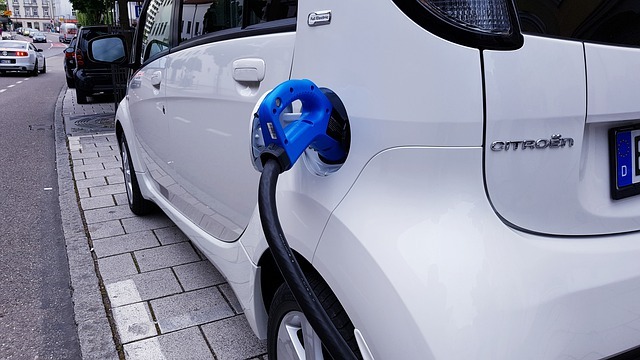
Hoy en día, el sector del vehículo eléctrico sigue en pleno proceso de desarrollo. Los fabricantes de vehículos están aumentando los modelos eléctricos que sacan al mercado, conscientes de la importancia de estar bien posicionados en el ranking de ventas de VEs (Vehículos Eléctricos) pero, sobre todo, transformar sus metodologías de diseño y fabricación para adaptarse a la tecnología eléctrica.
Por tanto, estos cambios implican una serie de nuevas oportunidades laborales que se pueden acometer por personas que posean conocimiento en vehículo eléctrico. Las oportunidades de negocio más importantes son:
- Desarrollo de pack de baterías.
- Desarrollo de nuevos inverters que permitan gobernar varios motores.
- Tecnología del motor en rueda y sistemas de regeneración en aceleración (además de en frenada).
- Vehículo autónomo.
- Sistemas de recarga de vehículo eléctrico.
1. Oportunidades laborales consecuencia de estos cambios
El auge de la tecnología eléctrica y su implantación en el mercado actual, implica una serie de nuevas oportunidades laborales que se pueden acometer por personas que posean conocimiento en vehículo eléctrico. Las oportunidades de negocio más importantes son:
- Desarrollo de pack de baterías.
- Desarrollo de nuevos inverters que permitan gobernar varios motores.
- Tecnología del motor en rueda y sistemas de regeneración en aceleración (además de en frenada).
- Vehículo autónomo.
- Sistemas de recarga de vehículo eléctrico.
1.1. Desarrollo de pack de baterías.
Todo fabricante de vehículos necesita un proveedor del pack de baterías. Actualmente, casi el 100% de las celdas que conforman un pack procede de China y Corea. Lo cierto es que es muy complicado (por no decir imposible o poco realista) intentar ser competencia de estos grandes de la química de las celdas de litio, pero sí que existe mercado para desarrollar e implementar el pack completo.Un pack de baterías es mucho más que comprar las celdas y empaquetarlas. La clave está (y es donde una empresa aporta valor) en desarrollar los siguientes aspectos:
Escoger la celda adecuada para cada tipo de aplicación.
Hay que tener en cuenta que una celda se diseña para suministrar su energía de dos maneras: mediante una intensidad de descarga muy alta durante unos segundos (limitando su capacidad nominal a valores más bajos que otras celdas) o limitar dicha descarga máxima, pero suministrando una capacidad nominal más alta. Esto, obviamente, posee efectos sobre la durabilidad de la celda. Por tanto, es necesario definir y ayudar a definir el objetivo de funcionamiento del vehículo, para escoger la celda más adecuada buscando siempre el compromiso entre intensidad de descarga (potencia máxima para alimentar los motores de tracción) y autonomía del vehículo. En este punto, también entran en juego tres conceptos más: masa de cada celda (por tanto, peso del pack), ciclos de carga/descarga del pack de baterías (durabilidad o vida media del pack) y tiempos de recarga.
Diseñar la envolvente (carcasa exterior del pack) adecuada a la necesidad de cada fabricante.
Teniendo en cuenta el espacio disponible y la estrategia de montaje de los diferentes módulos tanto para producción como para postventa. Sin perder de vista que esta envolvente (y en general, el pack) debe pasar la correspondiente homologación de vehículos.
Gestión térmica de la batería:
Este es uno de los principales caballos de batalla de un buen pack de baterías y es la diferencia fundamental entre proveedores. Un batería se calienta en descarga, con lo que debe ser refrigerada adecuadamente. Para ello es fundamental estimar como se van a descargar las celdas (es decir, estimar un modelo matemático de descarga) y desarrollar sistemas que sean capaces de predecir (en base a ciertas medidas realizadas por sensores en batería) los gradientes térmicos en el pack para ajustar la refrigeración de las celdas y lograr que trabajen siempre dentro de su rango de temperaturas de funcionamiento. Si una celda llega a su temperatura máxima de funcionamiento, el módulo al que pertenece se desconecta, con lo que se pierde capacidad de descarga o incluso de desconecta completamente la batería hasta que se refrigere adecuadamente. Y, por otro lado, está el proceso de carga, que igualmente genera un calentamiento del pack. Hay dos situaciones límite; un pack de baterías descargado y a elevada temperatura que es necesario cargar de inmediato, pero que no es posible iniciar por la temperatura elevada de sus celdas; un pack que se desea cargar a elevada velocidad y que se calienta hasta tal punto que es necesario para la carga. En consecuencia, esta gestión térmica es fundamental para el funcionamiento del pack.
En Europa hay pocas empresas que se dediquen al montaje de pack de baterías, estando el grueso de empresas en China. En España están comenzando a nacer algunas empresas que montan estos packs (existiendo algunas ya consolidadas) y otras empresas que trabajan para el sector industrial, tratan de incorporar a su cartera de productos, las baterías eléctricas de tracción de vehículos.
Teniendo en cuenta que los costes de producción son mayores en Europa que en China, es necesario diferenciarse y justificar ese coste, aportando valor al producto suministrado. Es aquí donde la ingeniería europea (y concretamente, la española) podemos ganar la batalla y ser capaces de ser proveedores de baterías para las plantas de fabricación de vehículos eléctricos en Europa.
1.2. Desarrollo de nuevos inverters que permitan gobernar varios motores.
Un driver (también denominado controlador, inverter o inversor) es un dispositivo electrónico que realiza dos funciones principales:
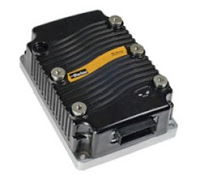
- Convierte la corriente continua del pack de baterías en una señal alterna trifásica necesaria para alimentar el motor eléctrico.
- Regula la velocidad y el par motor en función de las órdenes enviadas por la ECU motor.
Cada driver debe ser configurado para cada motor en concreto y debe tener unas especificaciones compatibles con el motor a controlar. De esta manera se necesita un driver por cada motor eléctrico y una programación específica para cada tipo de motor (en función de su tecnología de funcionamiento y del tipo de información que da para poder situar su posición).
Muchos fabricantes de controladores de motores eléctricos industriales, se están reconvirtiendo o asumiendo también el control de motores de tracción eléctricos, con lo que hay una necesidad creciente de profesionales especialistas en este tipo de controles y parametrizaciones.
A día de hoy, desde el punto de vista de un fabricante de vehículos, resulta un hándicap tener que instalar un inverter por cada motor. Esto tiene varias implicaciones:
- Aumento del coste total del vehículo.
- Necesidad de disponer de los espacios necesarios para su montaje.
- Aumento del número de cables en tensión que es necesario instalar en el vehículo.
- Dimensionamiento adecuado del sistema de refrigeración para incorporar a dichos controladores.
Uno de los retos pendientes de solventar (y que está solventando en el sector industrial) es que se puedan controlar todos los motores mediante el mismo controlador o, mejor dicho, mediante un único componente que disponga de las entradas y salidas necesarias para controlar hasta 4 motores eléctricos.
1.3. Tecnología del motor en rueda y sistemas de regeneración.
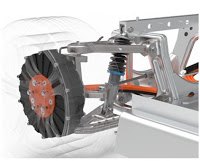
Las ventajas de esta configuración son las siguientes:
- Se elimina la caja de cambios, el diferencial y el palier (o transmisión), lo cual implica un descenso del coste del vehículo y de su peso.
- Al tener un motor en cada rueda, se puede gobernar al 100% la dinámica de tracción de cada rueda (independientemente del resto y de forma instantánea) y la gestión en curva del vehículo, pudiendo realizar las correcciones necesarias actuando sobre el par motor de cada motor (que es lo que se denomina torque vectoring).
- Se gana espacio interior en el bastidor (para emplearlo, por ejemplo, a la hora de disponer de un espacio extra para un mayor pack de baterías).
Como desventajas, podemos citar las siguientes:
- Aumento de la masa no suspendida del vehículo, lo que implica tener que reestudiar las vibraciones generadas en rueda sobre el vehículo.
- El motor está más expuesto a golpes y los cables de alimentación eléctrica al motor se deben rutear por partes móviles del vehículo (sistema de suspensión) además de tener más exposición a golpes de elementos procedentes de la carretera.
1.4. Vehículo autónomo
El coche autónomo es el gran objetivo del sector del automóvil en todo el mundo. Cada vez más conductores se plantean cuando les será posible viajar en el coche leyendo un periódico o echando una cabezada.
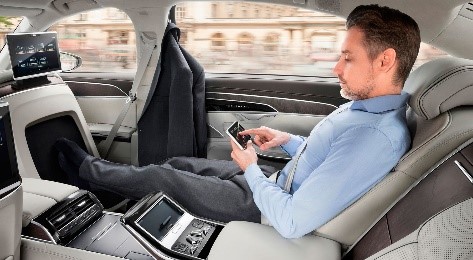
La evolución de la conducción autónoma se divide en 5 niveles o fases:
- El primero y el segundo son los niveles en los que nos encontramos actualmente. Son aquellos en el que los vehículos tienen ayudas en la conducción, tales como el frenado automático, el control de velocidad y de estabilidad. El nivel 2 se relaciona con un automatismo parcial y suele aplicarse a la circulación por autopista. El coche maneja cambio y pedales, frena y acelera para adaptarse a los cambios de ritmo del tráfico (como en el Nivel 1) e incluso toma curvas suaves, de radio amplio. Por ley, el conductor ha de mantener las manos en el volante, aunque sin ejercer fuerza, basta con apoyarlas. Pero sigue siendo el único responsable y debe permanecer atento en todo momento.
- La Fase 3 es la que está en actual desarrollo. En esta fase, el coche autónomo puede asumir todas las funciones de la conducción en determinadas situaciones.
- No es hasta la Fase 4, que el vehículo funciona totalmente autónomo, sin necesidad de conductor. Es aquí, donde las personas se convierten en meros pasajeros (eximiéndole de cualquier tipo de responsabilidad).
- Por último, la Fase 5 es la más ambiciosa. Los concept cars presentan habitáculos en movimiento, sin volantes ni otros elementos que controlen los pasajeros.
El Nivel 3 ya está listo, pero un reciente cambio legal en Europa limita su aplicación (se espera que se solucione a lo largo de este año). En EEUU y China sí funciona actualmente.
Los primeros modelos nivel 4 están previstos para 2021, aunque es probable que su operatividad se restrinja todavía a ciertos escenarios de conducción. Además, hay que alcanzar una fiabilidad de funcionamiento del 99% , con lo que la mayoría de los fabricantes siguen acumulando millones de kilómetros con sus modelos de prueba para afinar los sistema de Inteligencia Artificial y alcanzar esos registros de operatividad.
Por tanto, es un sector en el que se necesitan muchas horas de trabajo para perfeccionar este sistema.
1.5. Sistemas de recarga del vehículo eléctrico
Para lograr una penetración total del vehículo eléctrico, es fundamental que exista una infraestructura de recarga adecuada en términos de prestaciones y disponibilidad. Según datos extraídos de un informe elaborado por Deloitte, España necesita unos 90.000 puntos de recarga de acceso público en 2025 y 145.000 en 2030.
En España existen 4.545 puntos de recarga de uso público, de los cuales el 32% se encuentra concentrado entre Madrid (552 puntos), Barcelona (722) y Valencia (192). En otros países de Europa, las cifras son mayores. Países Bajos lidera el ranking con 9.559 puntos, Francia, le sigue con 8.585 y Alemania con 7.600.
Las compañías energéticas ya han tomado la iniciativa en esta transición hacia una movilidad más sostenible, lanzándose a la implantación de nuevos puntos y trabajando para mejorar aspectos como los sistemas de carga, que permitirán utilizar mayores potencias y, por tanto, ahorrar tiempo a los usuarios. Esto se complementa con la aparición de nuevas empresas especializadas en el diseño e instalación de puntos de recarga (tanto domésticos como públicos).
En consecuencia, este es un sector en pleno auge y del que se derivará mucha carga de trabajo en los próximos años.
2. Conclusiones
Hoy en día, la introducción del vehículo eléctrico es una realidad, donde tanto empresas como particulares van renovando gradualmente el parque de vehículos.
Esta nueva tecnología abre una serie de oportunidades de trabajo e innovación, entre las que destacan las siguientes:
- Diseño de nuevas plataformas (bastidor) para vehículos eléctricos.
- Desarrollo de nuevas tipologías de celdas generadoras de energía.
- Diseño y fabricación de pack de baterías.
- Desarrollo de nuevos inverters que permitan gobernar varios motores.
- Apuesta por el concepto de motor en rueda e implementación de la lógica de control.
- Mejora en los sistemas de regeneración de energía para la carga de baterías.
- Avance en el vehículo autónomo.
- Creación de estaciones de recarga.
- Planificación energética sostenible para la fabricación de baterías y para su recarga.
- Formación de técnicos especialistas e implantación de nuevos sistemas de seguridad de riesgo eléctrico en fábricas de montaje y talleres de reparación.