La industria 4.0, un camino hacia el ahorro energético
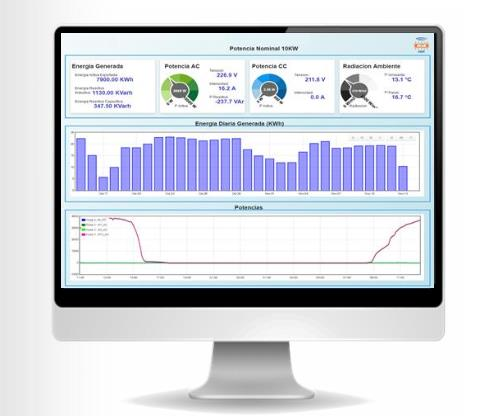
El concepto de Industria 4.0 corresponde a un nueva metodología de organizar los medios de producción. El objetivo es poner en marcha un gran número de fábricas inteligentes dotándolas de las tecnologías más avanzadas, se busca además, aumentar la cantidad y calidad de la producción con un coste mucho menor, ahorrando energía y apoyando la modernización del empleo.
La digitalización de las empresas se considera la 4ª revolución industrial después de las impulsadas por la máquina de vapor, la electricidad y la automatización. Numerosos estudios indican que la integración de la digitalización en las cadenas productivas van a acelerar el proceso de producción en un 20%, la economía española ocupa el puesto 14 por volumen de PIB, pero baja al puesto 45 en lo que a digitalización se refiere, por ello se hace necesario, para que no quedar rezagados en esta carrera por la denominada 4ª revolución industrial, que se establezcan políticas gubernamentales que incentiven las inversiones en el sector privado para la adaptación a la industria 4.0.
En este nuevo paradigma el consumo energético será uno de los factores claves, ya que representa uno de los grandes valores competitivos entre empresas, por lo que aquellas que más consigan reducirlo verán garantizada su rentabilidad económica y por tanto su supervivencia en el mercado, apostando por un modelo de sostenibilidad.
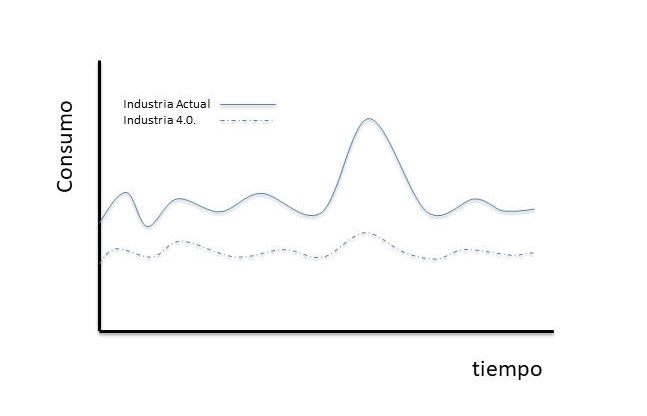
Por tanto el control, análisis y optimación del consumo energético de los equipos, debe estar presente en todo momento en la adaptación de la empresa a la industria 4.0., y para ello se deber de seguir los siguientes pasos fundamentales:
- Adaptación de equipos: Se debe eliminar o reducir al máximo el número de equipos a los que no se les pueda graduar su rango de funcionamiento, es decir, los equipos todo-nada. Para ello se debe implementar mejoras tecnológicas que permitan variar el consumo de los equipos en función de las necesidades del proceso.
- Adquisición de datos: este paso es fundamental, se deben monitorizar de forma continua los consumos energéticos de todos los equipos, eliminando todos los registros manuales que se puedan estar realizando. De igual forma es necesario disponer la monitorización de todos los datos del proceso que abordan los equipos (temperatura, caudal, densidad, …) ya que los mismos afectan de forma significativa a los valores de consumo.
- Procesamiento de datos: la información obtenida debe manejarse y analizarse para una mejor compresión e interpretación, incluyendo la validación de las señales de los sensores y los atributos de estimación o extracción.
- Toma de decisiones: se deciden las acciones a tomar basadas en los resultados, diagnóstico y la aplicación de la inteligencia artificial mediante algoritmos de control y/o redes neuronales, estas se aplicarán en tiempo real y estarán encaminadas a buscar las optimización del consumo energético.
Dentro de la fase de la toma de decisiones, se deben de buscar los siguientes objetivos:
- Optimización de consumo en los procesos: Al disponer de una monitorización continua de los parámetros del proceso se debe establecer para cada estado y momento el rango de funcionamiento óptimo de los equipos donde el coeficiente capacidad productiva-consumo energético sea máximo.
- Adaptabilidad al flujo del proceso: Con la información disponible en tiempo real se deben obtener modelos dinámicos del proceso con mayores velocidades de respuesta. De esta forma se podría , por ejemplo, en caso de producirse una congestión o cuello de botella puntual, en una parte del proceso, poder reducir de forma inmediata el rango de funcionamiento, y por tanto el consumo eléctrico, de los equipos que se encuentren aguas abajo de dicha congestión mientras esta dure evitando el sobreconsumo de los equipos al trabajar a un régimen superior al necesario.
- Optimización de la estrategia de mantenimiento: El control del proceso y la aplicación de la inteligencia artificial nos permitirán conocer el consumo teórico de los equipos en función de los parámetros del proceso y el estado del equipo, por lo que en caso de detección de desviaciones superiores sobre dichos valores nos permitirán la detección de averías de forma temprana conjuntamente con la aplicación del mantenimiento inteligente, que es otro de los pilares de la industria 4.0.. Esto nos permitirá establecer una estrategia de mantenimiento que tenga en cuenta el coste económico del sobreconsumo del equipo que presenta una avería para decidir el momento de detección del mismo para su reparación.
¿Cómo empiezo a optimizar y transformar?
- Seleccionar puntos de mejora: dónde podemos ganar más o dónde podemos ahorrar costes.
- Identificar qué información es necesario colectar para lograr esas mejoras
- Elegir la tecnología necesaria para digitalizar y almacenar la información para la mejora de los procesos.
- Aplicar la inteligencia artificial para la mejora de los procesos.
La inteligencia artificial está cada vez más presente en todos los ámbitos de la Industria 4.0 y en el sector energético es una de las herramientas con mayor potencial.
Artículo publicado en el Nº22 de Dínamo Técnica, marzo de 2018.
Autores:
Javier Basanta García. Miembro del Foro Enerxético de Galicia.
Feliciano Fraguela Díaz. Dirección de obra en Mantenimiento y Servicios, Tecman S.L. Profesor asociado de la UDC.
Alfredo Sanchez Córdoba. CEO de IDAB.